New equipment requires special care while awaiting installation
Balancing today’s lengthy lead times/supply chain issues with the need to keep critical operations running smoothly, petrochemical and refining plants are hedging their bets by proactively ordering new or replacement equipment (e.g., pumps and motors) a year or more in advance of the anticipated install date. Upon early arrival on-site, the equipment is typically staged in a remote field, where it is likely exposed to damaging elements that threaten the integrity of the components. Therefore, preservation of this standby equipment is of utmost importance to avoid premature failure on start-up and to reduce mean time between failures (MTBF).
Oil Mist Technology – How it Works
As part of your asset strategy, Oil mist technology helps protect new equipment while it awaits implementation. Simply stated, this mixture of air and oil is a cool, dry, contaminant-free mist applied to moving parts, like bearings, for prolonged life. A centrally located generator combines the oil and air, producing micro-size particles to allow easy conveyance over a long distance (i.e. approximately 600 feet in any direction). As it reaches its destination, the air/oil mixture passes through a “reclassifier” that turns it into a wet substance for lubricating purposes. Note that certain components, such as gears inside gearboxes, may still require an oil sump for “purge misting.” Regardless of the pump or motor type, there is a solution to make the oil mist approach workable.
Case Study – Oil Refinery, Philadelphia, PA
Oil mist lubrication systems have many uses, whether in standby mode or during operation. A real-life scenario returned investment to a Pennsylvania refinery’s cooling tower for the purchase of an oil mist lubrication system, in less than one year. Two gearbox failures were eliminated per year (saving $50,000 in repair costs for each gearbox), and oil spill risk was reduced to zero. Overall, the oil mist successfully mitigated excessive water contamination that was previously responsible for erosion, rust, and sludge formation in gearbox reservoirs. Read the full case study here.
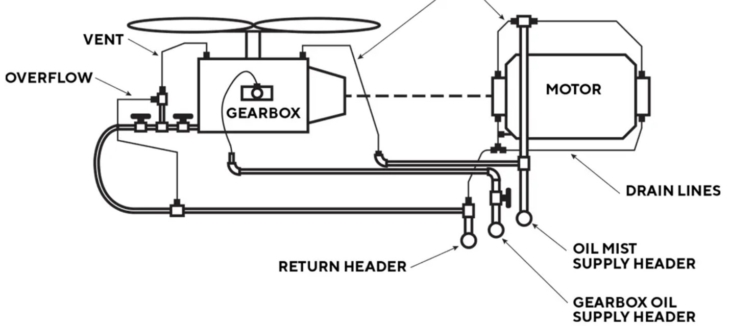
Typical cooling tower gearbox setup with oil mist lubrication system.
Conclusion
Best-in-class facilities that excel in equipment reliability and financial profitability realize the cost benefits of including oil mist lubrication system as part of their routine maintenance program for all machines on their premises, running or not. The alternative is to continue doing just-in-time repairs and essentially let facilities become “rust buckets” over time.
Contact Allied Reliability for more information about oil mist lubrication. www.alliedreliability.com